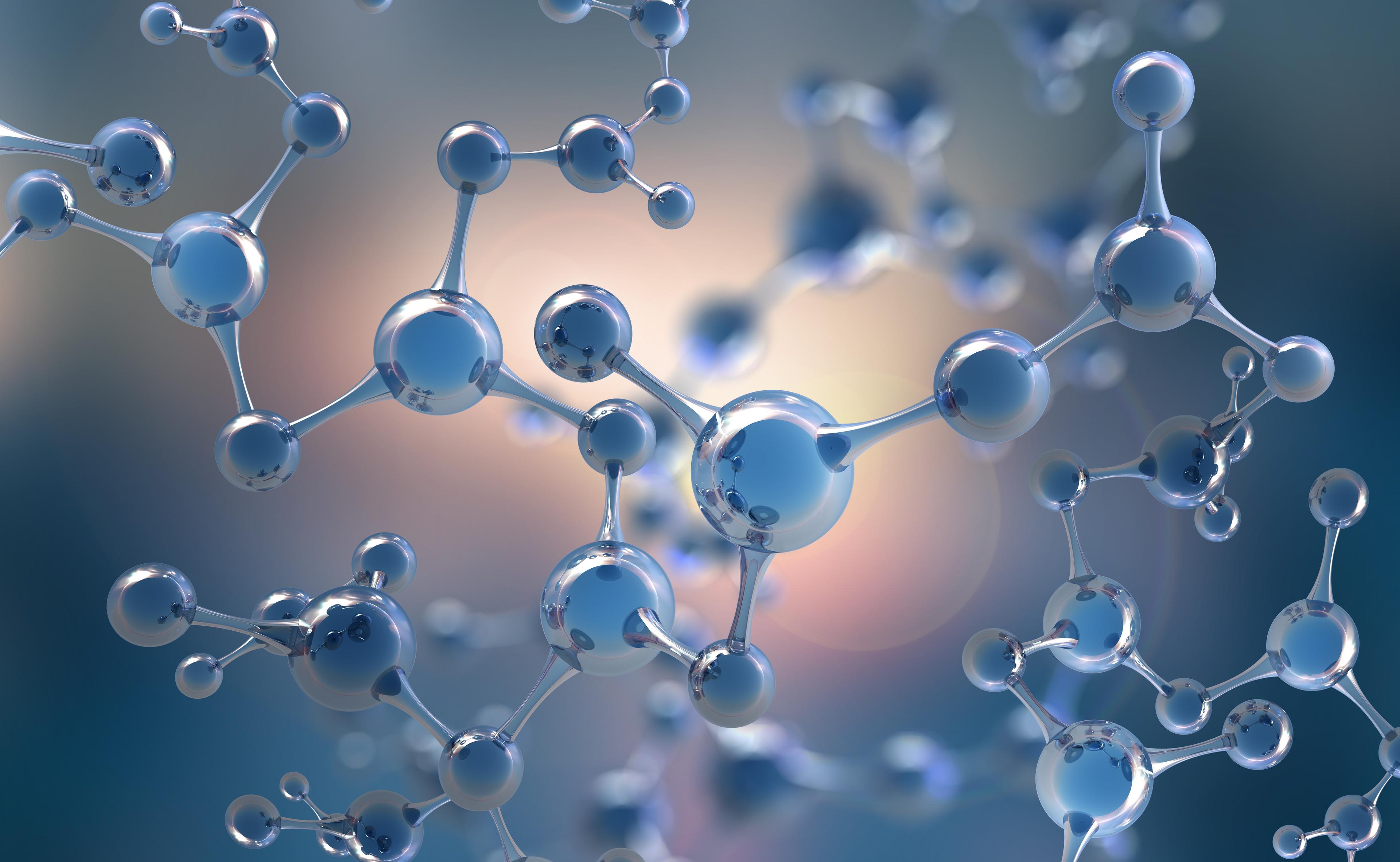
Molecules, mass, and finding the right energy balance: A deeper look into the methanation process
February 19, 2024
Reading time: 5 min
TES uses the Sabatier reaction to produce e-NG from green hydrogen and recycled CO2. Let’s take a quick look into how it works and how we ensure high efficiency.
e-NG or electric natural gas is a green synthetic methane and TES’ game-changing key product. It will play a pivotal role in driving widespread decarbonization and make it easier for heavy industry to engage with the green transition.
We sat down with TES CTO, Jens Schmidt, to get the full picture on why TES opted to make e-NG, how it gets made, and how the Sabatier process is part of a chain that may be one of the most efficient and scalable ways to produce green fuels.
e-NG is produced using mature, reliable technologies
TES generates green hydrogen in locations where producing renewable energy is most cost-effective. The hydrogen molecule is very high energy by weight but has a very low density according to volume. To make it easier to transport, it has to be bound to another molecule.
TES employs a well-established methanation process known as the Sabatier reaction. Named after the French chemist Paul Sabatier, who discovered the reaction with his colleague Jean-Baptiste Senderens in 1897 and won the Nobel for it in 1912, it’s an exothermic (heat-releasing) reaction that enables the production of methane from the building blocks of hydrogen and carbon dioxide.
Here’s how it works. In a methanation reactor, hydrogen and carbon dioxide are exposed to elevated pressures of around 30 bar at a heat of around 400 degrees celsius in the presence of a nickel catalyst. This causes the molecules to react which produces methane and water. The equation that describes the Sabatier reaction is:
CO2 + 4H2 → CH4 + 2 H2O
It doesn’t take a keen chemist to notice that half of the hydrogen used in the reaction ends up as water but, as TES CTO Jens Schmidt explains, the Sabatier equation only tells part of the story.
“If you look at the mass balance, half of your hydrogen goes into water, but we're talking about transporting energy and on an energy level, it looks completely different. We recover about 83% of the lower heating value that goes into the reactor and that's what really counts. So the energy we put in to produce the hydrogen is preserved with over 80% in that molecule that is so easy to transport and use.”
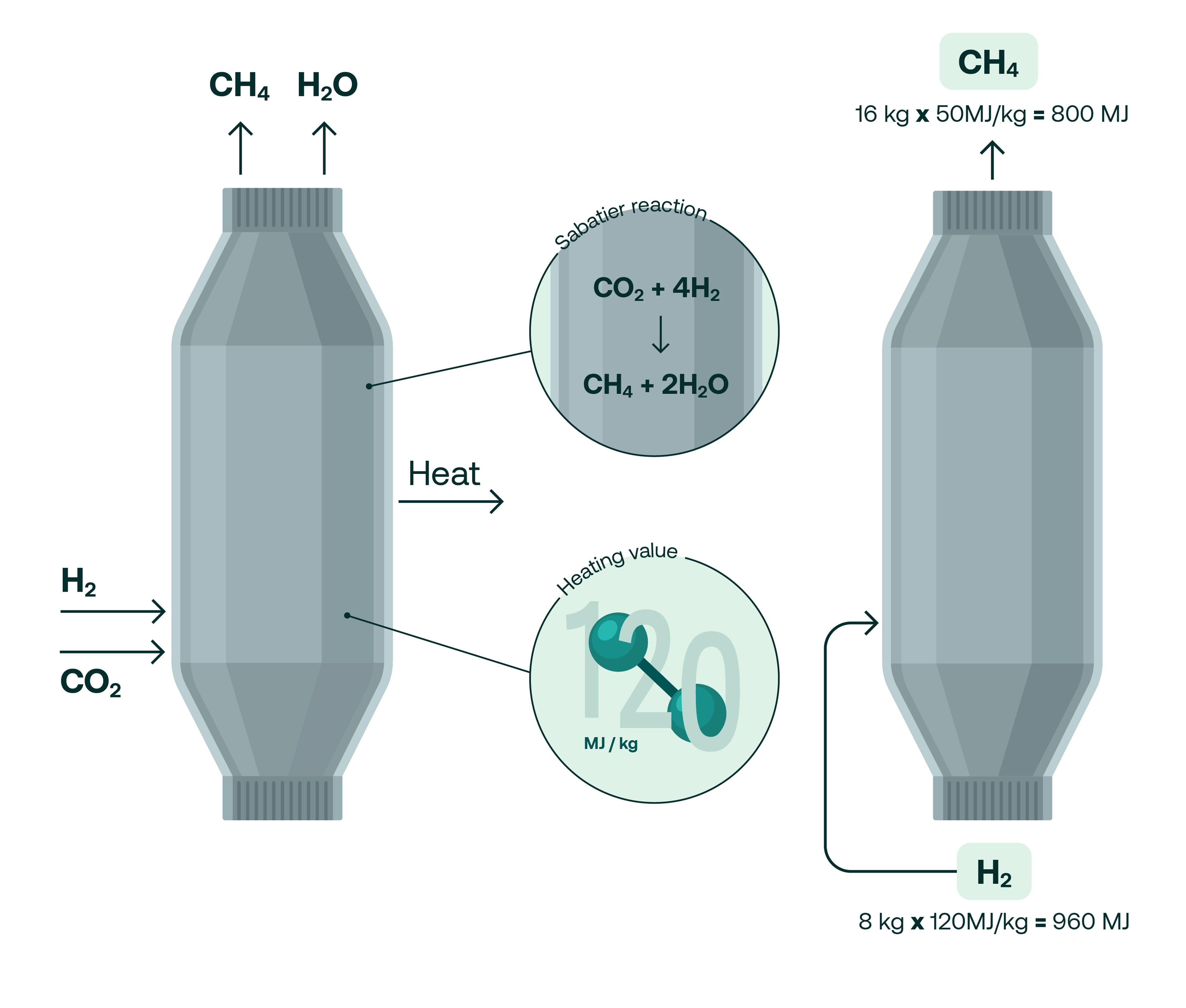
The remaining 17% of the energy is rejected from the reactor as very high-temperature heat. To make their processes as efficient as possible, TES harnesses this waste heat and turns it into steam which can then be used to generate electricity or fed directly to high temperature electrolyzers which reduces the total amount of fresh electricity needed for the process.
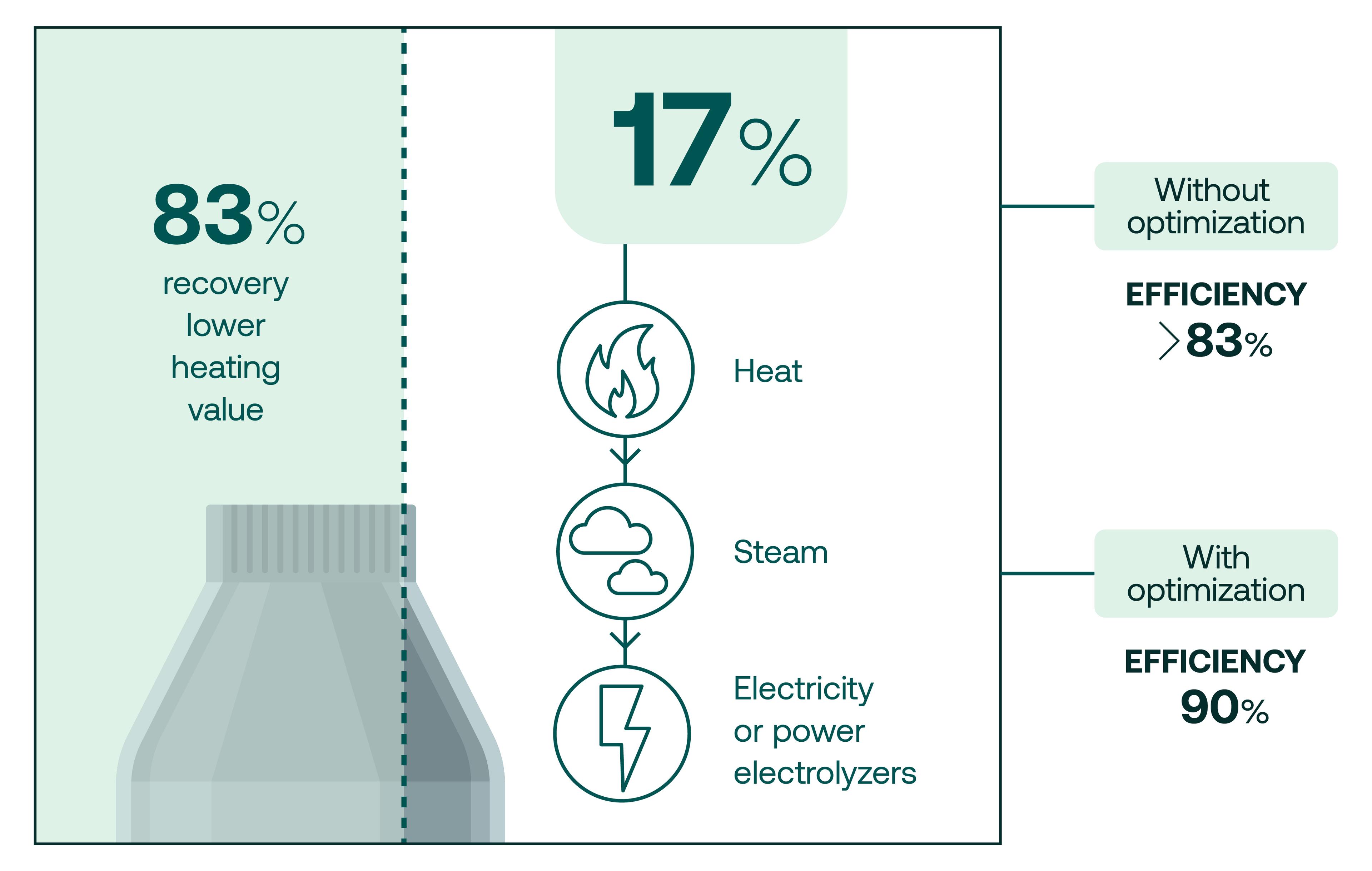
“Thereby we can reach efficiencies that are even higher than the 83% you get off the shelf, and we have a credible pathway and technical solutions to bring that to way above 90% efficiency”, says Schmidt. The 50% of hydrogen that ends up as water is recycled in the electrolyzer to reduce freshwater intake by almost half. Reducing water consumption in this way is particularly important in regions with high solar energy potential.
Combining sustainability with bankability
TES is keen to ensure every process is as efficient as possible, for both sustainability and bankability reasons. Luckily, the most sustainable methods also make good economic sense.
Schmidt explains: “If you look at the grand scheme of things, what really counts is emissions profile and climate impact, efficiency along the cycle, existing infrastructure, how quickly you can reach your customer and, at the end of the day, what is economically feasible. We've studied all [possible hydrogen] derivatives extensively and they’re all pretty much on par when it comes to the efficiency of producing them.”
Where e-NG crucially differs from other hydrogen derivatives is the technical readiness of the infrastructure, the simplicity of serving it to customers, and ease of transportation.
“Compared to ammonia, for example, the volumetric energy density [of e-NG] is about 1.7 times higher. So to transport the same amount of energy with ammonia, you would need 1.7 ships where you need only one ship with e-NG. The same holds for methanol and all the other derivatives. They simply need more space to be transported.”
The fastest route to a green transition
At COP28 which took place at the end of 2023, 118 governments committed to tripling renewable energy production by 2030. Already in early 2024, we’re seeing a sharp uptick in the amount of renewable energy being produced globally which is helping to drive down emissions.
Because e-NG doesn’t require expensive infrastructure upgrades or the discovery of new technologies, it can be produced and supplied immediately to customers who want to engage with the green transition but don’t have the capacity to slow down production or to wait for new systems to be installed.
e-NG is the fastest, most efficient way to support heavy industries’ net-zero goals and to encourage a widespread gradual conversion to green energy. TES works hard to build efficient, pragmatic processes based on mature technologies that ensure the best possible use of materials, infrastructure, money, time, and energy.
As TES CTO Jens Schmidt says, “We've looked carefully at all the different alternatives. For us, combining CO2 and hydrogen to make synthetic methane is the best way to transport and reach our customers through existing infrastructure and distribution systems.”